CICERO PERSPECTIVE
Why Deferred Maintenance Is Becoming a Strategic Risk for Mid-Market Manufacturers
What to consider
In boardrooms across the country, the conversation around mid-market manufacturing strategy is dominated by familiar buzzwords: reshoring, digital transformation, ESG targets, and talent pipelines. But beneath these high-profile initiatives lies a much quieter—and in many cases, more immediate—threat to operational viability: deferred maintenance.
For decades, many manufacturers managed to delay maintenance expenditures with minimal fallout, banking on reliability and redundancy to cover the gaps. But the economic, regulatory, and operational environment of 2025 is no longer so forgiving. Today, deferred maintenance is evolving from an engineering problem to a full-blown strategic risk—with implications for productivity, investor confidence, and long-term enterprise value.
A Risk Decades in the Making
According to a recent report by Plant Engineering, over 40% of U.S. manufacturers admit to delaying maintenance on critical equipment in the past 12 months. Some estimates peg the annual nationwide backlog of needed industrial maintenance at over $150 billion. This isn’t just about worn-out conveyor belts—it’s aging HVAC systems, neglected filtration units, uncalibrated safety systems, and electrical infrastructure decades past its intended service life.
Until recently, these were considered tolerable trade-offs—acceptable delays in the pursuit of capital efficiency. But three compounding factors have now turned deferred maintenance into a ticking time bomb:
- Labor attrition: Retirements among seasoned technicians have outpaced the entry of new skilled labor, leaving facilities vulnerable to gaps in institutional knowledge and reactive-only maintenance cultures.
- Regulatory tightening: Environmental and safety inspections have intensified, particularly in sectors with historical non-compliance patterns, exposing firms with outdated infrastructure to penalties or even shutdowns.
- Private equity pressure: Mid-market manufacturers are prime targets for acquisition, but hidden maintenance liabilities can undermine post-close value realization and delay integration timelines.
A Case in Point
Consider the case of a fictionalized, composite firm: “Midwest Polymers,” a privately held plastics manufacturer with four facilities and $85M in annual revenue. Over the past seven years, the company repeatedly deferred roughly $2.3 million in recommended maintenance and facility upgrades—ranging from worn conveyor systems to outdated fire suppression equipment.
In 2024, a minor mechanical fault escalated into a full plant shutdown after a sprinkler failure triggered a non-compliance audit. The result: three weeks offline, $1.4 million in lost revenue, $450,000 in emergency repairs, and two canceled contracts with large buyers—nearly $8 million in total fallout. That’s a nearly 3.5x multiplier on what proactive maintenance would have cost.
From Technical Debt to Strategic Blind Spot
So why hasn’t maintenance received the strategic attention it deserves?
Because in many organizations, it’s still treated as an engineering line item, not an input into enterprise risk or corporate planning. This siloed thinking leads to a consistent under-prioritization of investments that aren’t visibly broken—until they break everything.
Moreover, even sophisticated due diligence processes often fail to account for the real extent of deferred maintenance. Capital expenditure projections typically assume upkeep, not recovery.
Strategic Responses We’re Seeing
Forward-thinking operators and investors are beginning to reframe maintenance as a strategic asset rather than a sunk cost. Some emerging best practices include:
- Asset Condition Indices (ACIs) integrated into board reporting structures—not just for facilities, but for entire value streams.
- Predictive monitoring systems (thermal imaging, vibration analytics, pressure differential sensors) that deliver ROI within 18 months, especially in temperature- or motion-sensitive operations.
- Maintenance Readiness Indices used as early indicators in M&A diligence, influencing everything from valuation to hold period strategy.
- Executive compensation plans tied to facility uptime and readiness—not just EBITDA.
If your operations strategy doesn’t explicitly include a plan for surfacing, quantifying, and reducing deferred maintenance, you’re flying blind in at least one critical quadrant of risk. The solution isn’t just to spend more—it’s to treat maintenance with the same rigor and intentionality as procurement, compliance, or financial planning.
That means asking questions like:
- What is our facility’s true backlog of maintenance, and what’s the worst-case exposure?
- Where does deferred maintenance sit on our enterprise risk map?
- How do we quantify and communicate maintenance risk to leadership, boards, and potential investors?
Deferred maintenance isn’t a technical footnote—it’s a strategic fault line. And in a world defined by constrained capital, fragile supply chains, and high-performance expectations, it may just be the most overlooked threat to your company’s future resilience.
Ignoring it is no longer a tactical decision. It’s a strategic failure.
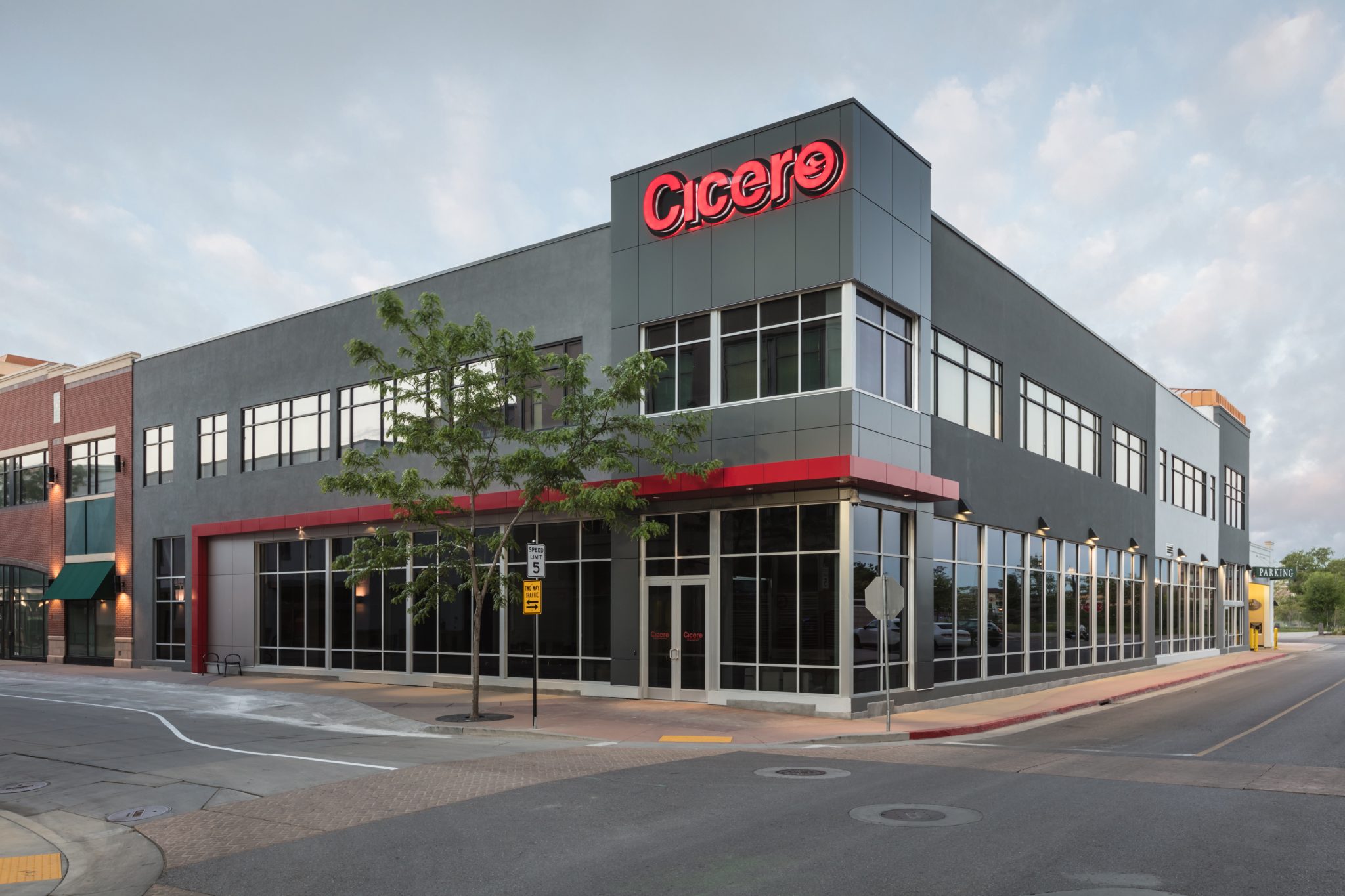
Start a Conversation
Thank you for your interest in Cicero Group. Please select from the options below to get in touch with us.